As the concept of quality from design (QualitybyDesign) continues to deepen, pharmaceutical production process development and pilot testing are increasingly valued by the pharmaceutical industry, aiming to solve the widespread use of pharmaceutical production processes from experimental amplification to mass production. The status quo of the problem.
     Compared with the traditional wet granulation, the dry granulation has the granular raw materials directly prepared to meet the user's requirements, without any intermediates and additives. After granulation, the product has uniform particle size and the bulk density is significantly increased, not only to control pollution, It also reduces powder and energy costs, improves material appearance and fluidity, facilitates storage and transportation, and controls many advantages such as solubility, porosity and specific surface area. It is especially suitable for wet mixed granulation and one-step boiling granulation. .
     Based on the above two points, Germany Alexanderwerk company designed a new, WP120Pharma dry granulation machine is suitable for research and development laboratory and trial, it can be widely used in pharmaceutical R & D or small batch production, shown in Figure 1 .
1 device characteristics
Because in the process of drug development or pilot testing, in order to save costs, the production volume is usually relatively small, which is more obvious in some costly biopharmaceuticals. The WP120Pharma dry granulator has a minimum processing volume of only 5g/ batch and granulation of 8 to 40kg/h under continuous production , which makes the equipment fully compliant with the requirements of drug development and pilot testing.
     In addition, the variety needs to be changed frequently in the R&D or pilot test, and the press cantilever mounting of the device makes it easy to disassemble and clean the equipment between different varieties. For the R&D experiment or pilot test, the device has certain mobility and flexibility. The device is designed as a mobile unit and integrates the control and operation panel directly on the device ( as shown in Figure 2 ) so that it can be different. The place of use is quickly put into production.
     In addition to the above characteristics, the WP120Pharma is designed to meet the regulatory and technical requirements of the pharmaceutical industry: (1) The granulation device and the power unit are spatially separated; (2) The vertical alignment of the pressure roller eliminates the influence of gravity; (3) Equipment Designed to comply with cGMP ; (4) Two-stage screening granulation system to ensure the production of granules that meet the requirements; (5) Made of medical grade stainless steel; (6) All non-metallic materials meet FDA- related requirements; (7) Automated PLC ; (8) optional: CIP; (9) optional feature: an electronic record (in compliance with the relevant requirements 21CFRPart11); (10) optional: sound means; (11) may be carried out in accordance with customer demand requires a standard (URS) design.
2 structure and principle
2.1 structure
The WP120Pharma dry granulator is mainly divided into a granulating device and a power device, and the two parts are completely isolated in space. The granulating device is mainly divided into 8 modules ( as shown in Fig. 3 ) : 1 is a feeding hopper; 2 is a screw feeding system; 3 is a pressing unit, a pressing roller; 4 is a pre-pressing unit; 5 is a sampling port; 6 is a two-stage screening granulation system; 7 is a sampling port; 8 is a particle outlet.
     This equipment is different from the conventional granulator. The addition of 5 and 7 sampling ports is precisely the need to take frequent and multiple sampling when analyzing process parameters in drug development or pilot testing.
2.2 Principle of granulation
2.2.1 Rolling pressure
     The basic principle of the rolling process during dry granulation is very simple. The dry powder or fine crystalline material is extruded into rolls by a press roll, and the quality of the flakes determines the quality of the final granules.
     The rolling pressure of the ordinary dry granulator and the gap of the pressure roller are relatively fixed, and the difference between different materials and different batches of the same material cannot be considered. The WP120Pharma dry granulator uses the latest roll control technology. The equipment's control equipment can adjust the fluctuation of any physical properties between different materials and different batches of the same material ( such as local unevenness ) , making the dry granulation process parameters (such as the processing amount, the density of a sheet, roll pressure, speed, etc.) can be accurately, repeatedly adjusting to efficiently produce high-quality particles.
     In addition, there is a clear, modular separation between the feed and roll processing of the apparatus, and the screw feed system 2 delivers the powder directly to the press roll 3 so that the roll press process does not affect the screw feed system. The initial suppression process is shown in Figure 4 .
2.2.2 granulation
The granules usually have corresponding particle size requirements. Generally, the above lower limit forms that the particles exceeding the specified particle size and the insufficient particle size do not meet the requirements. After the rolling treatment, the pre-compressed flakes are obviously larger than the upper limit of the final particle size, and only the pulverization of the granulation system can produce the final granules. Moreover, the downstream processing of the final granules ( e.g., tableting ) requires that the particle size fluctuations of the granules be controlled to a small extent.
     In response to this problem, the granulation system of WP120Pharma adopts a two-stage diagonal design. The first stage is a pre-granulation device, and the second stage is a final granulation device. The control system separately adjusts the two-stage granulation system to produce Particles with relatively stable particle size. As shown in Figure 5 .
3 is more suitable for GMP
     From the consumer's point of view, purity is the most important attribute of medicines; from the perspective of pharmaceutical manufacturers, equipment should have certain flexibility in function, especially for experimental or pilot equipment. The WP120Pharma dry granulator meets both of these requirements – clean and flexible. First of all, WP120Pharma is a completely closed dry granulation system, which can reduce the dust pollution in the production process, thus reducing the risk of pollution and pollution. Secondly, the equipment adopts modular design, and the whole granulation device can use only a small amount of Tools. It can be disassembled for easy cleaning of all modular units and the screw and press rolls can be easily replaced to suit different granulation tasks.
4 conclusion
Currently, WP120Pharma has been widely used in laboratory or pilot plants to determine process parameters in subsequent mass production. On process parameters measured in the apparatus can be easily amplified to large machines, such as manufactured WP200Pharma Alexanderwerk. It can be said that WP120Pharma is an ideal experimental dry granulator in the current drug development or pilot test.
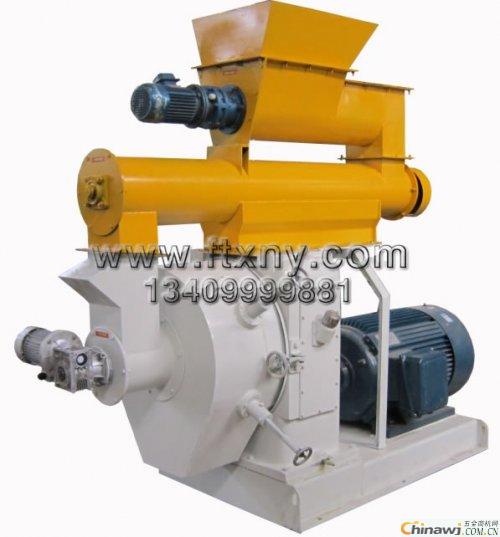
Freezer Cold Storage Room,Cold Storage Room,Freezer Storage Room,Portable Cold Room
LONG TERM ELEC. CO., LTD , https://www.longterm-hvac.com