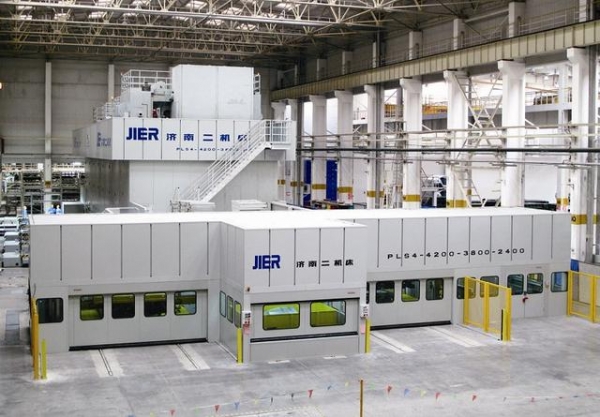
Data Sheet: Jinan No. 2 Machine Tool is a stamping production line produced by Shanghai GM Dongyue Automobile Co., Ltd.
The Jinan No. 2 machine tool provided five press lines for Ford, one installed in a factory in Kansas City, USA, and the other four installed in the Ford headquarters plant, replacing its original 23 old production lines. Zhang Zhigang, chairman and general manager of Jinan No. 2 Machine Tool, is the best narrator of the “China Independent Story†of large-scale presses.
    Editor's Note: The 13-storey "large press" of 13-storey building is forging out the landing gear and main beam of the aircraft; the network control system consisting of thousands of software becomes the brain and nerve of the high-speed train; the offshore oil rig, Looking forward to rolling up the waves of the South China Sea; 4000 tons of cranes will raise arms for large nuclear power plants.
Major equipment manufacturing is related to the country's lifeline and national security. People who pay quietly in this field are worthy of the name of "national engineer." They focus on the big powers that represent the country's core manufacturing capabilities; their careers hold the backbone of the national economy.
On the occasion of the 65th anniversary of the founding of the People's Republic of China, Xinhuanet and "Looking East Weekly" jointly launched a large-scale report "Honor! National Engineer" to introduce readers to the major technical equipment manufacturing projects representing "China's creation" and their core teams. .
China, the world's largest automobile manufacturing country, has finally won a place in the four major automobile manufacturing processes of stamping, welding, painting and final assembly. The stamping technology, which is the first in the process, has been developed and harvested by Chinese companies.
In the workshop of Shanghai GM Dongyue Automobile Company in Yantai, Shandong Province, it takes only 4 seconds for a steel plate to enter a stamping machine to become a door.
In other words, these machines with the logo of Jinan Second Machine Tool Group Co., Ltd. can produce 15 body stamping parts including door every minute. The fastest speed of stamping machines previously supplied to Chinese auto companies by Germany was 13.5 per minute.
By the summer of 2014, 80% of the automobile production enterprises in China were from Jinan No. 2 machine tools. The other three processes require high-end equipment to be imported from abroad.
As the chairman and general manager of Jinan No. 2 Machine Tool, Zhang Zhigang is the best narrator of this “China Independent Storyâ€. Like many major achievements in equipment manufacturing, this is also a story related to national dignity. However, in Zhang Zhigang's view, “a large-scale fast and efficient automatic stamping production line†is just the beginning of this story.
He mentioned that he led the team to Iran in 2001: because of the sanctions, the best German and Japanese companies in the industry did not participate. The Chinese originally felt that they were very grasped, but the result was that Korean companies won the bid.
"South Korea, this company has to say its technology, we are not convinced, and the size of the company is not as big as us. The Iranians told me that when you see that we are running a Chinese brand car on Tehran Street, you will win the game." "Zhang Zhigang has been pondering on his way back to China. "We Chinese should be arguing."
Ten years later, Jinan No. 2 Machine Tool won the first production line of Ford Motor Company in Detroit. “After winning the bid, I walked on Detroit Street and saw the famous cars in the country. I am not proud of it.â€
Two years later, after winning the sixth production line of Ford's Kentucky plant in the United States, Zhang Zhigang “feeled pride and prideâ€. However, as he said, this "international competition" that shapes the image of China's equipment manufacturing is a huge challenge.
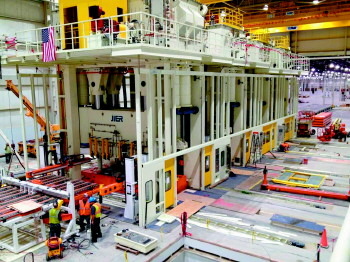
Data Sheet: Jinan Second Machine Tool Group's production line at Ford's Kansas plant in the US
     "Printing banknotes" from China
In terms of composition, cars are usually divided into four parts: engine, chassis, body and electrical equipment; according to the car manufacturing process, it is divided into four major processes: stamping, welding, painting and final assembly.
Specifically, firstly, by stamping--flattening the steel sheet material, according to the corresponding shape requirements, under the action of 4 to 5 presses, the excess part is removed to form a side cover of the car, four doors and two covers, and the like. .
Secondly, the welding robot welds all kinds of stamping parts to form a body; then, the painting process paints the body to prevent rust and beauty; finally, the body, tires, lights, sounds, seats, etc. The parts are assembled and become the whole vehicle. Stamping is the first step, including the door, top cover, side panels, columns, hoods, etc. More than 70% of the body parts are stamped from stamping equipment. The pressure of the press causes the steel sheet to be stretched or hard pressed, the steel plate is opened, and the useless portion is cut. As the first of the four major automobile processes, the press line is also known as the “printing line†and is a key equipment for automobile manufacturing equipment.
The reason for the 2011 bid was that Ford wanted to replace the stamping equipment that the German stamping company produced for its early years.
The Jinan No. 2 machine tool provided five press lines for Ford, one installed in a factory in Kansas City, USA, and the other four installed in the Ford headquarters plant, replacing its original 23 old production lines.
This transformation is even more expensive than the new factory built by Ford.
As the person in charge of procurement, Ford's head of stamping equipment planning said in an email to Jinan No. 2 Machine Tool that if there is a problem with this project, his career "will end here."
The production efficiency of stamping machines is a key factor in ensuring quality.
The Jinan No. 2 machine tool provided five press lines for Ford, one installed in a factory in Kansas City, USA, and the other four installed in the Ford headquarters plant, replacing its original 23 old production lines. Zhang Zhigang, chairman and general manager of Jinan No. 2 Machine Tool, is the best narrator of the “China Independent Story†of large-scale presses.
German companies have kept records of 13 records per minute for nearly 10 years. Although the Korean company reported a lower price in this bid, Ford finally decided to hand over the press line to Jinan No. 2 Machine Tool. Soon, Jinan Second Machine Tool won another contract for four production lines.
The stamping machine is the heart of the entire assembly line. For example, accuracy directly determines whether the door can be closed perfectly. One of the highest standards of stamping machine tools is to make the error between the product and the drawing close to zero.
“Now the ordinary production line can produce 4,000 to 5,000 pieces per day, but our production line is twice as efficient as the ordinary production line.†Li Chao, deputy general manager of Jinan Second Machine Tool Press and Automation Company, said that the most What is difficult to control is the punching force.
“The speed should be low, the strength should be stable, and the production efficiency should be improved.†He said that under a certain pressure, the slower the speed, the better the stamping quality; otherwise, the steel plate is easily cracked or wrinkled.
The use of pressure to shape metals is not uncommon in industrial manufacturing. For example, hydraulic machines and hydraulic presses can show stable strength and good stretching effect, but the perfect control of this power is long-term and low-efficiency. In the industrial world, almost only mechanical pressure can meet the speed and efficiency requirements.
At the end of 2011, the Ford project was first accepted, and the other party raised four or five questions and opinions. The Chinese personnel are puzzled, how can there be so many problems. The other party said that you should be satisfied. When the Germans first gave the Ford project, they were faced with more opinions and questions.
By June 2014, when Ford's sixth production line was inspected, the other party raised only 40 questions.
After the Ford project, world-class car companies such as Mercedes-Benz, Audi and Chrysler have visited the Jinan Second Machine Tool.
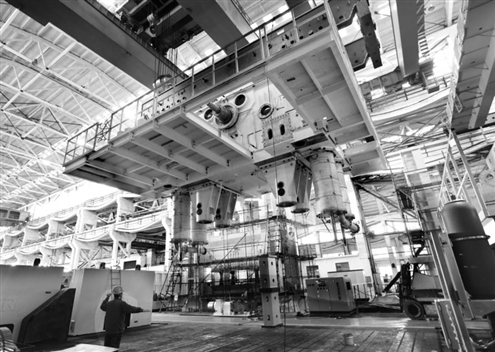
Data Sheet: Workers of Jinan No. 2 Machine Tool Group are carrying out large-scale lifting
Zhang Zhigang was born into a family of troops and had special feelings for the country and the army. In addition to undertaking a number of major military projects, the Jinan II machine tool of more than 5,000 people also has a reserve camp, which has 4 companies under its jurisdiction.
“As a car enthusiast, I have driven almost all brands of cars.†Zhang Zhigang said that if he chooses, performance is the primary factor. “I like to push back when starting. When the engine reaches 3500 rpm, there are still A powerful torque car."
In 1977, Zhang Zhigang entered the university during the first resume of the college entrance examination and studied mechanical manufacturing.
At that time, China's automobile industry was on the way. Although there were brands such as Liberation and Red Flag, the output was extremely low. Most of the cars on the street were imported. Zhang Zhigang said that it would not stand on the streets of Detroit until a few decades later. He still can't calm down, because there is no shadow of Chinese manufacturing in those shuttle cars.
As early as around 1953, under the guidance of the former Ministry of Machinery Industry, Jinan No. 2 Machine Tool began to enter the field of planer and stamping. The company was founded in 1937 and was once a military factory of the National Government. It is known as one of the “18 Arhat Factory†in the history of China's machine tool industry.
On the basis of "24 horsepower and 40 hp diesel engines, agricultural liberation brand waterwheels, ash mixers, railway spikes and other products", the first large gantry in China was born in the workshop of Jinan No. 2 Machine Tool Plant in 1953. planer.
"Created the dragon gate planer and started the first shot", which became the loudest slogan of Jinan at that time.
"At that time, the technology was from the Soviet Union. The 200-ton press was already advanced." Zhang Shishun, deputy general manager of Jinan Second Machine Tool Group Co., Ltd. told us that although there were technical guidance from Soviet experts, the process of manufacturing itself was still difficult.
As a major achievement of the pressure machine tool at that time, it was mostly used in tractor manufacturing. From the 1950s to the 1970s, pressure machine tools were as rampant as the entire automotive industry.
“At that time, domestic cars, whether they were passenger cars or commercial vehicles, did not form batches.†Zhang Shishun said, “The market size is small, and it is difficult for the press industry to support large-scale R&D investment.â€
In the early 1980s, with the reform and opening up, Jinan No. 2 Machine Tool began to cooperate with a stamping company in the United States. In Zhang Shishun's view, the other party has realized that China will be a very huge market.
After graduating from university, in the first 10 years of Zhang Zhigang's design as a design engineer, the Chinese side provided a cooperation model between the market and the US to provide technology, so that the Jinan No. 2 machine tool developed rapidly. Shanghai Volkswagen Santana and Guangzhou Peugeot have used the production line of Jinan No. 2 Machine Tool.
By the early 1990s, the Chinese auto industry accelerated, and the Jinan No. 2 machine tool introduced a full set of technology from the United States. At the time, that was the world's most advanced stamping technology. "We have entered the era of cars from the era of tricycles," said Zhang Shishun.
Before and after this, Jinan No. 2 Machine Tool provided the first production line for FAW Audi.
In the new century, China's automobile industry has gradually prospered. After nearly 20 years of working in Jinan's second machine tool, Zhang Zhigang became an "engineer" from an engineer and foreign trade director to 2003.
At that time, the climax of state-owned enterprise reforms that shocked the entire country in the late 1990s was over, but Zhang Zhigang still carried out reforms against the contingent of cadres after taking office.
Through the appointment system and competition, the original Jinan No. 2 machine tool with 130 cadres has only 70 cadres left. Today, Zhang Zhigang still does not want to mention the pressure that the nearly half of the cadres at the time "laying off" brought him.
The reform was an important event that later promoted the impact of Jinan No. 2 Machine Tool on the world of stamping: the importance of technical cadres was mentioned at an unprecedented height, and today 7 of the 8 executives are technically born.
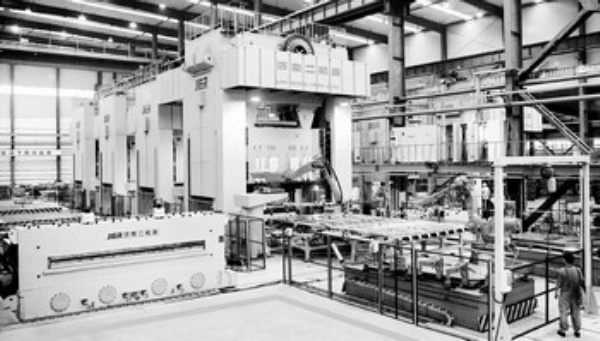
Data map: China's first fully automatic stamping production line produced by Jinan No. 2 Machine Tool
     Bit by bit detail
With the improvement of China's industrial strength, companies such as Jinan No. 2 Machine Tool have been difficult to cooperate with foreign companies. In the past, the other party valued their cost advantages and gradually shifted to the competition level.
For example, the Dongyue press line in Yantai, Line 1 and Line 2 are the result of cooperation between Jinan No. 2 Machine Tool and German companies. By the time General Motors planned to update its third production line in 2002, German companies were aware of the threat and refused to cooperate. "To the fourth line, we are the products we have done alone, and the fifth is also." Zhang Shishun said that in addition to Korean cars, domestic car manufacturers are customers of Jinan No. 2 machine tools.
In the 1990s, Jinan No. 2 Machines produced less than 200 body stampings per hour when it received US machine tool technology, averaging about three per minute.
In the new century, the domestic pressure machine tool industry is “coming togetherâ€, “We are American technology, and some companies have introduced Japanese technology.†Zhang Shishun said that although many companies were doing it at the time, the ideas were similar. Only Jinan Second Machine has mastered the technology, and other companies only got the drawings.
By 2009, the stamping speed of Jinan No. 2 machine tool increased to 12 per minute.
"It’s not a day’s work to get the Ford production line. The whole process is made up of bits and pieces of detail.†As early as 2004, Ford sent someone to visit. “The overall impression is OK, but if you let him The purchase was obviously not practical at the time." Zhang Shishun said.
At the end of 2009 after the completion of Dongyue Line 4, the Ford Brazil plant and the Australian factory were sent to China for inspection. Zhang Shishun felt that at that time, the attitude of the other party was "can buy".
In 2010, Ford sent another person to visit Jinan. At this time, Jinan No. 2 Machine Tool has two advantages: low cost and shorter delivery time. Previously, in 2009, China surpassed the United States for the first time to become the world's largest auto producer. More than 80% of the automotive exterior parts are produced from the stamping equipment manufactured by Jinan No. 2 Machine Tool.
The progress of domestic independent intellectual property equipment has greatly reduced the cost of automobile manufacturing. There are also views that the low-cost, high-efficiency production brought about by localized heavy-duty equipment will allow cars to enter ordinary Chinese families at least three years in advance.
Although it is one of the "three major stamping equipment manufacturers in the world", the stamping machine is only one type of product of Jinan No. 2 machine--metal forming machine tool, which can be used by metal deformation; the other is metal cutting machine tool. That is, the parts are cut.
Zhang Zhigang hopes that CNC cutting machine tools can become the next international product of Jinan No. 2 Machine Tool. Because they are also extremely critical equipment in important fields such as defense military, aerospace, and equipment manufacturing.
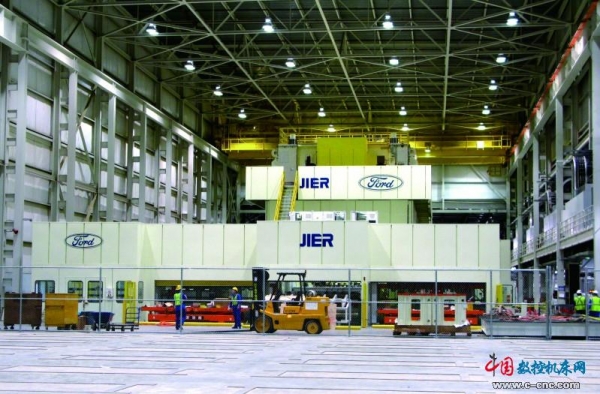
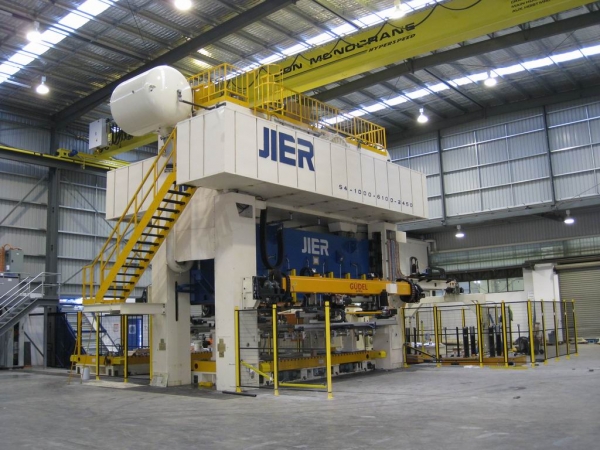
1000t heavy duty servo press
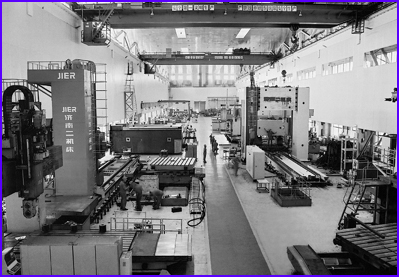
The picture shows the assembly site of Jinan No. 2 Machine Tool CNC Machine Tool
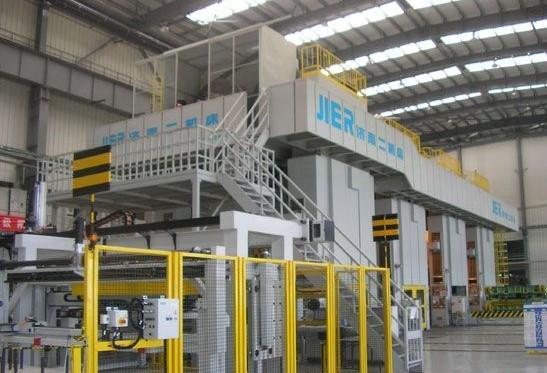
Find here online price details of companies selling Mini Excavator Final Drive. Get info of suppliers, manufacturers, exporters, traders of Mini Final Drive .
You may call it a Mini Final Drive or a Mini Excavator Travel Motor With Gearbox, but no matter the name, when your Excavator Final Drive needs to be replaced, you can`t afford to have your machine down for long.
We are a professional manufacturer of hydraulic accessories for crawler excavators Professionally provided aftermarket customers with various brands of crawler excavator Final Drive, Travel motor, Travel Gearbox, Swing Device , Swing Motor , Swing Gearbox ,hydraulic pump, main Control Valve and other accessories.Strictly controlling the quality acceptance of each product Standards to ensure high-quality qualified export of each product.At the same time, we can customize the production services of the products through the drawings according to customer needs, and make every effort to make the perfect product in the mind of each customer.
If you want to know more about our products in more detail, please click on the product details to see more information about product quality, price, packaging, transportation, etc., or you can directly click on Contact Now on the page to talk to us directly. Looking forward to starting long-term business cooperation with you!
Mini Excavator Final Drive,Mini Final Drive,Mini Travel Device,Mini Excavator Travel Motor With Gearbox
Jining Juheng Hydraulic Machinery Co., Ltd. , https://www.juheng-cn.com