Graphite and diamond-like carbon films are an important type of solid lubricants, which have excellent lubrication and wear resistance in the atmosphere, but these materials rapidly fail in a high vacuum environment, thus severely restricting their application in the space field.
The Research Group of Wear and Surface Engineering of Lanzhou Institute of Chemical Physics, Chinese Academy of Sciences has devoted many years to the study of space lubricating materials. Recently, they discovered that two-dimensional graphene structure can solve the problem of vacuum lubrication failure that graphite has faced for a long time. Graphene is a basic component of a graphite layered structure, which transforms the three-dimensional structure of graphite into a two-dimensional thin-film structure. Due to the strong large delocalization π on the two-dimensional surface, the two-dimensional graphene sheet can spontaneously form an oriented layered structure under the action of π-π, thus avoiding the disorderly accumulation of polycrystalline graphite and the surface dangling bonds. The problem of exposure. In the friction process, the distance between the graphene nanosheets becomes closer, the frictional interface forms a highly ordered, straight layered orientation structure, and the parallel planes have a weak van der Waals force, and interlayer slip plays a leading role, making it It exhibits an ultra-low coefficient of friction at macroscopic contact. The graphene layer has extremely high mechanical strength and is not easily damaged. The low-friction state is maintained for a long time and wear is minimal. At the same time, graphene has excellent electrical and thermal conductivity characteristics. The results of this study lay the foundation for the development of new types of ultra-low friction, conductive and thermally conductive integrated space lubrication films (Applied physics letters 110 (2017) 073101).
On this basis, they introduced the graphene structure into the amorphous carbon film, utilizing the method of external field induced growth, using graphite as the magnetron sputtering target source, high-purity methane and argon as the reactive gas source, and in the external field (including Magnetic fields, electric fields, catalysts, high-activity plasmas, etc.) form graphene target precursors under a comprehensive induction condition, and are then sputtered into the carbon film in the form of molecules, atoms, or clusters of atoms to form graphene intermediates. Ordered nanostructured carbon-based thin film materials. The vacuum tribological performance of this film has achieved a great breakthrough. The friction coefficient is very low (less than 0.01) and the wear life is greatly improved. The current maximum reported in the literature is 1×105 revolutions. Under the same test conditions, the film reaches 8.5×105. The transfer has increased by nearly one order of magnitude (ACS Appl. Mater. Interfaces 8 (2016) 6639). Researchers have further solved the technical problems of stress in the film and firm bonding of various substrates through gradient surface layer, surface texture, and other surface/interface structure designs, which greatly promoted carbon film as a solid lubricant in space. Applications in the field (RSC advances 5 (2015) 8904, Tribology International 95 (2016) 298; 101 (2016) 395; and 71 (2014) 82, Tribol. Lett. 64 (2016) 24; 52 (2013) 371; and 49 (2013) 47, J. Vac. Sci. Technol. A 34 (2016) 031504, Vacuum 115 (2015) 23-30, J. Phys. D: Appl. Phys. 47 (2014) 235301 and 46 (2013) 425301, Surf. Coat. Technol., 236 (2013) 438, Proc. Inst. Mech. Eng. Part JJ. Eng. Tribol., 227 (2013) 729, Appl. Surf. Sci., 284 (2013) 165- 170).
The series of research work has been supported by the National Natural Science Foundation of China (51405474, 51472250, U1637204, and 51275509), the National Basic Research Program of the People's Republic of China (973 Program 2013CB632300), the Western Youth Scholars of the Chinese Academy of Sciences (Academy of Sciences), the Class A Program, and the “Young Innovation Promotionâ€. The long-term support for the "Training Project for Talents (2016368)".
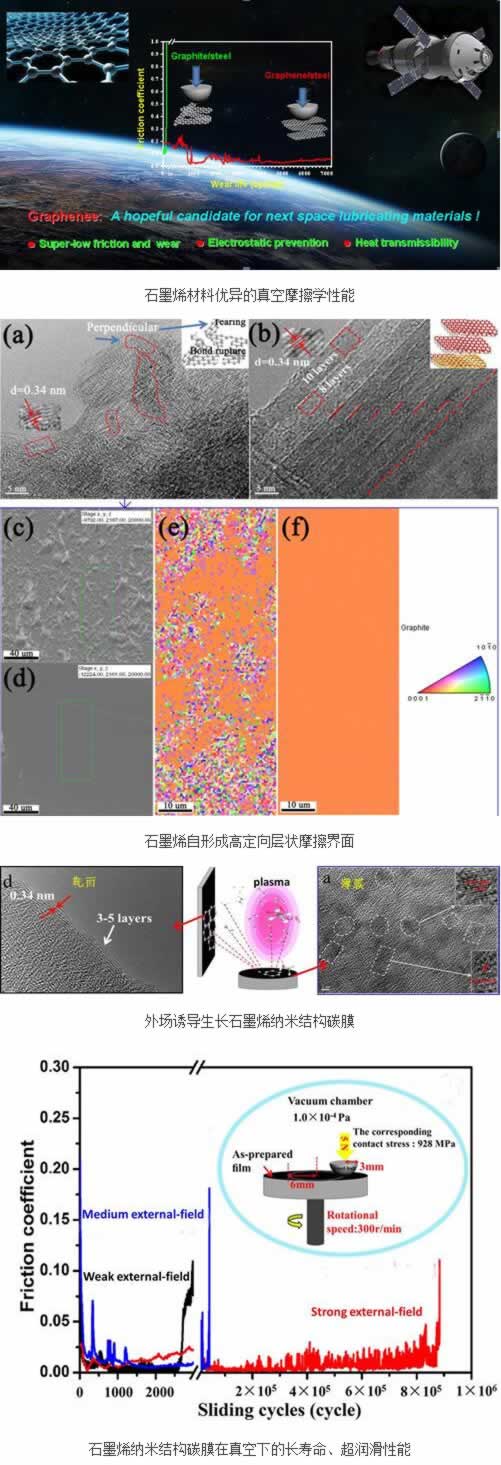
Ring-Grooved Lock-Bolt,Ring-Grooved Lock Bolt,Ring-Grooved Bolt Latch,Ring-Grooved Barrel Bolt Latch
KD METALS (JINGJIANG) CO.,LTD , https://www.toprivet.com