With the application of new tooling techniques, manufacturers can focus on cutting time costs, reducing auxiliary man-hours, and achieving break-even points in tool investment in a matter of hours in many machining applications.
How should we measure the technological advancement of tool products? How to measure success in business and career? No matter how you answer these questions, the answer is always related to some measure of time (for example: how long it takes to produce a tool, how much money the company makes each year, how much you earn per hour). Of all the things related to manufacturing, time is the biggest factor affecting profitability and improving company capabilities.
For mold processing techniques (such as machine tools, CAD/CAM, tools, materials, etc.), the technology you are using today is outdated. The concept of next-generation machine tools and tools has been researched and developed, and is entering the production application stage. These new ideas will ultimately affect the way the entire mold industry is manufactured.
While technology is constantly changing and moving quickly, and at a price, it is measurable. Once you prove that these technologies are worthwhile, you should invest in them. This article focuses on tooling techniques and how these tools can reduce overall manufacturing costs.
Among all the techniques used in daily mold processing, cutting tools are the least expensive, but they are also the most expensive for companies to buy. As an employee, you need to have a general understanding of how an boss or purchasing person evaluates an investment; as a boss, when determining the value of a tool (or any other technology), you must look at the big picture, not just the price. So the right question is not "What is its price?" but "How much return can I get by applying this technology?"
Investing in tools can bring returns to the business very quickly. By introducing new tooling techniques, the metal removal rate is greatly increased, resulting in improved processing capabilities.
Tool cost
Tool costs can also be saved with new tooling technology. Tool manufacturers who develop tooling products with the latest technology can provide economical and better machining solutions by developing stronger tools and inserts. By applying the latest carbide insert technology, it is possible to produce tools and inserts with more cutting edges and higher strength for better use of carbide materials.
Simple process
The process of introducing new tooling techniques is not necessarily complicated, and companies can often benefit immediately after a tool upgrade. When introducing new tool technology, you only need to establish a working relationship or cooperation relationship with the tool professional technician. These tool specialists have access to a large number of machining application examples and can be a valuable resource for continuously upgrading and updating tools with new and emerging technologies.
Applications
In order to improve the processing efficiency of a project, a tool and die manufacturer needs to shorten the overall cycle time of the shop to produce more workpieces in a shorter period of time. Through a partnership with a tool supplier, they are able to acquire some of the latest tooling technologies.
The material to be processed is annealed AISI/SAE 4140 low alloy steel (alloying element content less than 5%). In order to rough out the mold substrate, it is necessary to carry out heavy-duty rough milling of the workpiece by ramp milling and groove milling. After analyzing the machining requirements, the tool supplier recommended a sleeve mill designed for rapid metal removal (FMR) machining as a possible solution. The short tooling time, long tool life and ultra-high feed rate make it ideal for roughing. It uses a special type of triangular insert that can feed up to 3.5 mm per tooth. This unique insert geometry forms a large arc cutting edge structure that allows the tool to achieve high feed machining with large chip loads per tooth. In addition, the bottom of the insert is designed as a cylinder that can be clamped into the mating holes of the insert, allowing the insert to withstand large cutting forces for milling at ultra-normal feed rates. With this structural design, the clamping rigidity of the blade is greatly improved, thereby eliminating most of the stress normally applied to the fastening screw. Since the cutting force acts on the spindle in the axial direction, it contributes to an improvement in stability during processing. These design features allow the tool to achieve high metal removal rates, which increases overall project efficiency.
With this advanced tool, the productivity of the tooling shop is greatly improved, the cutting speed is maintained at 128m/min, and the cutting depth is maintained at 1.27mm. At the same time, the feed rate of the table increased from 1270mm/min to 6528mm/min, which was more than 5 times; the feed rate per tooth was also increased from 0.5mm/rev to 2.0mm/rev; the average chip thickness was from the time of using the original tool. 0.23mm increased to 1.45mm. Even with this greatly improved cutting parameter, the number of workpieces that can be machined per cutting edge is doubled (from 0.1 to 0.2), and the machining time per cutting edge is stable for 15 minutes. The total cutting time of the machining project has been reduced from approximately 16 hours in the past to approximately 4 hours.
In this processing project, the shortening of working hours not only helps to reduce the processing cost, but also allows the tooling workshop to accept additional processing projects. For manufacturers, time is an important resource that can have a major impact on the business. With the application of new tooling techniques, manufacturers can focus on cutting time costs, reducing auxiliary man-hours, and achieving break-even points in tool investment in a matter of hours in many machining applications.
How should we measure the technological advancement of tool products? How to measure success in business and career? No matter how you answer these questions, the answer is always related to some measure of time (for example: how long it takes to produce a tool, how much money the company makes each year, how much you earn per hour). Of all the things related to manufacturing, time is the biggest factor affecting profitability and improving company capabilities.
For mold processing techniques (such as machine tools, CAD/CAM, tools, materials, etc.), the technology you are using today is outdated. The concept of next-generation machine tools and tools has been researched and developed, and is entering the production application stage. These new ideas will ultimately affect the way the entire mold industry is manufactured.
While technology is constantly changing and moving quickly, and at a price, it is measurable. Once you prove that these technologies are worthwhile, you should invest in them. This article focuses on tooling techniques and how these tools can reduce overall manufacturing costs.
Among all the techniques used in daily mold processing, cutting tools are the least expensive, but they are also the most expensive for companies to buy. As an employee, you need to have a general understanding of how an boss or purchasing person evaluates an investment; as a boss, when determining the value of a tool (or any other technology), you must look at the big picture, not just the price. So the right question is not "What is its price?" but "How much return can I get by applying this technology?"
Investing in tools can bring returns to the business very quickly. By introducing new tooling techniques, the metal removal rate is greatly increased, resulting in improved processing capabilities.
Tool cost
Tool costs can also be saved with new tooling technology. Tool manufacturers who develop tooling products with the latest technology can provide economical and better machining solutions by developing stronger tools and inserts. By applying the latest carbide insert technology, it is possible to produce tools and inserts with more cutting edges and higher strength for better use of carbide materials.
Simple process
The process of introducing new tooling techniques is not necessarily complicated, and companies can often benefit immediately after a tool upgrade. When introducing new tool technology, you only need to establish a working relationship or cooperation relationship with the tool professional technician. These tool specialists have access to a large number of machining application examples and can be a valuable resource for continuously upgrading and updating tools with new and emerging technologies.
Applications
In order to improve the processing efficiency of a project, a tool and die manufacturer needs to shorten the overall cycle time of the shop to produce more workpieces in a shorter period of time. Through a partnership with a tool supplier, they are able to acquire some of the latest tooling technologies.
The material to be processed is annealed AISI/SAE 4140 low alloy steel (alloying element content less than 5%). In order to rough out the mold substrate, it is necessary to carry out heavy-duty rough milling of the workpiece by ramp milling and groove milling. After analyzing the machining requirements, the tool supplier recommended a sleeve mill designed for rapid metal removal (FMR) machining as a possible solution. The short tooling time, long tool life and ultra-high feed rate make it ideal for roughing. It uses a special type of triangular insert that can feed up to 3.5 mm per tooth. This unique insert geometry forms a large arc cutting edge structure that allows the tool to achieve high feed machining with large chip loads per tooth. In addition, the bottom of the insert is designed as a cylinder that can be clamped into the mating holes of the insert, allowing the insert to withstand large cutting forces for milling at ultra-normal feed rates. With this structural design, the clamping rigidity of the blade is greatly improved, thereby eliminating most of the stress normally applied to the fastening screw. Since the cutting force acts on the spindle in the axial direction, it contributes to an improvement in stability during processing. These design features allow the tool to achieve high metal removal rates, which increases overall project efficiency.
With this advanced tool, the productivity of the tooling shop is greatly improved, the cutting speed is maintained at 128m/min, and the cutting depth is maintained at 1.27mm. At the same time, the feed rate of the table increased from 1270mm/min to 6528mm/min, which was more than 5 times; the feed rate per tooth was also increased from 0.5mm/rev to 2.0mm/rev; the average chip thickness was from the time of using the original tool. 0.23mm increased to 1.45mm. Even with this greatly improved cutting parameter, the number of workpieces that can be machined per cutting edge is doubled (from 0.1 to 0.2), and the machining time per cutting edge is stable for 15 minutes. The total cutting time of the machining project has been reduced from approximately 16 hours in the past to approximately 4 hours.
In this processing project, the shortening of working hours not only helps to reduce the processing cost, but also allows the tooling workshop to accept additional processing projects. For manufacturers, time is an important resource that can have a major impact on the business.
Our products ranges:
LED aquarium lights for fish tanks,corals,saltwater tank,marine tank with reef,coral,sps,lps,fish,etc;
LED plant grow lights for agricultural lighting;
Our Coral Reef LED Aquarium Light is popular in led market,cause its elegant outlook and its high quality and competitive price.
Key Features
1.The lifespan is over 50000 hours,low maintenance costs.
2.Energy conservation,saving over 80% energy than the traditional HPS.
3.High light efficiency,90% of the light will be absorbed by the aquatic plants,while just 8%-10% to the HPS.
4.Build-in cooling system,could solve the heat dissipation excellently.
5.Built-in power supply, CE approved, No setup required, just simpler and safer plugs directly into AC85V-264V, no reflector & ballast needed.
Item Display
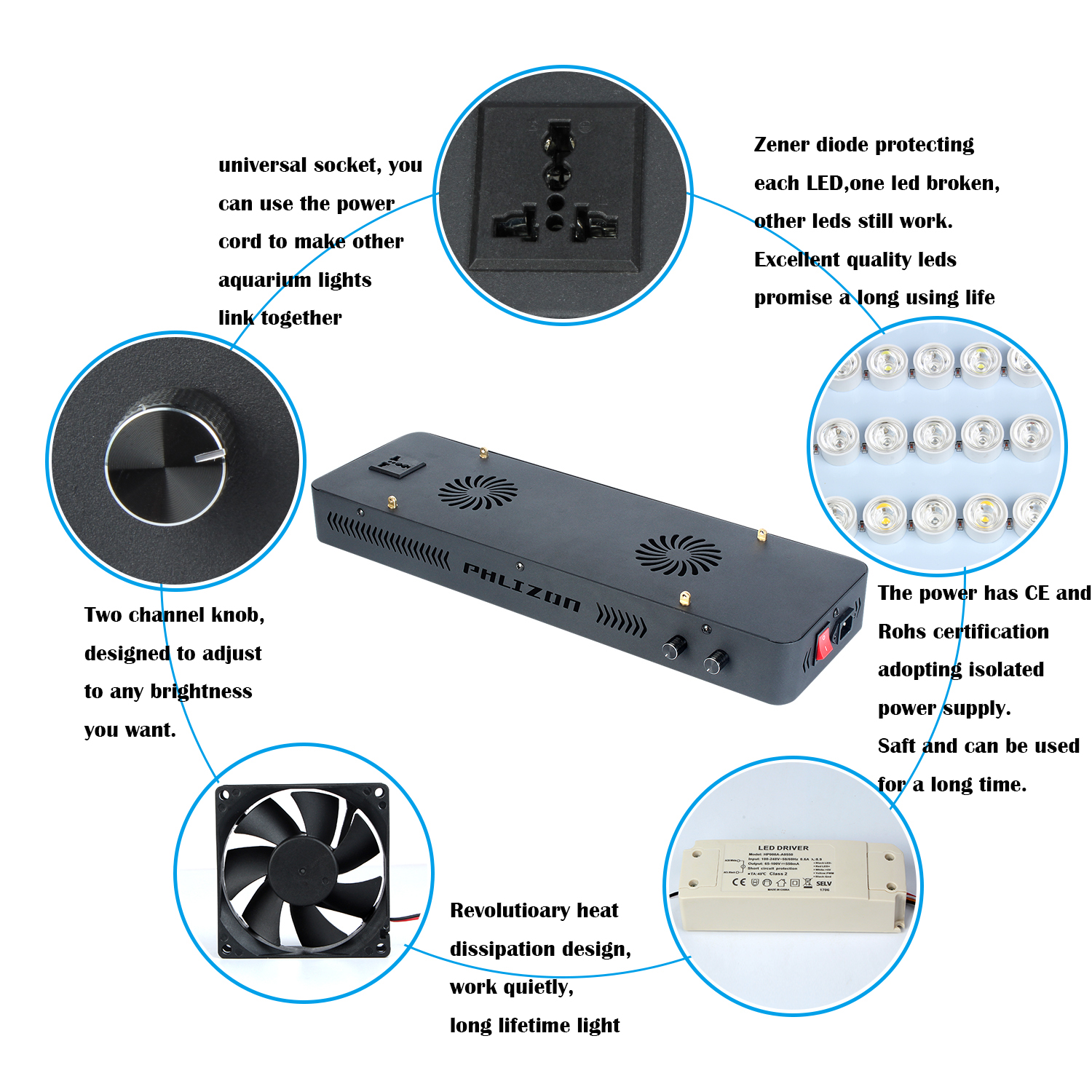
Convenient in using lights at the same time.
Package Include
1 X LED Aquarium Light
1 X Free Hanging Kit
1X Free Power Cord
Quality Control systems and after-sales
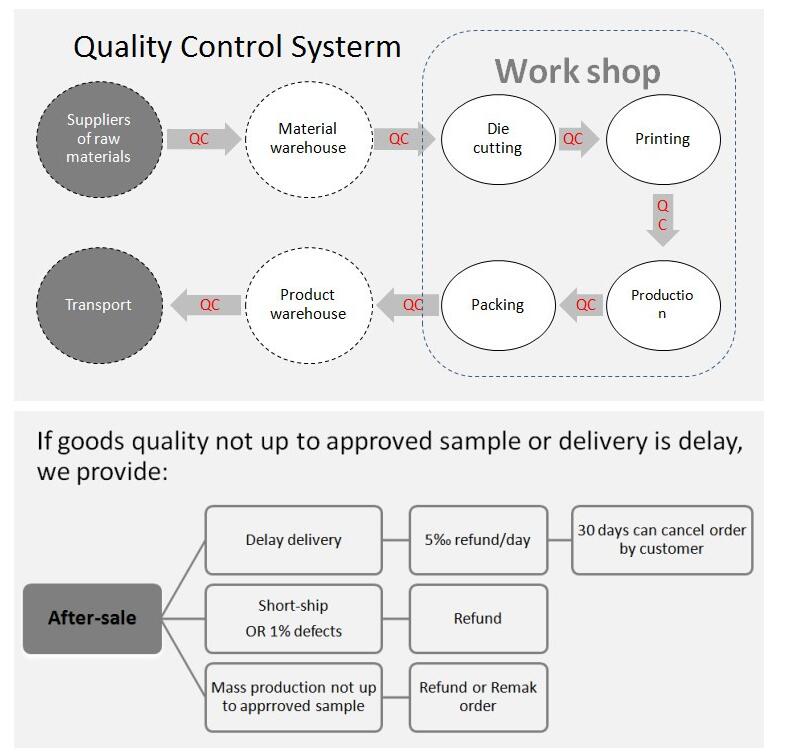
All the lamps have passed strict quality examination and are packed carefully before shipping.In order that our customers get high quality lamps,we attach importance to every details.
Application
1. coral reef lighting,fish tank lighting,coral reef tank lighting
2. aquarium lighting,aquarium art,aquarium shop,aquarim centre
3. fish bowl lighting,fish lighting,freshwater lighting,saltwater lighting
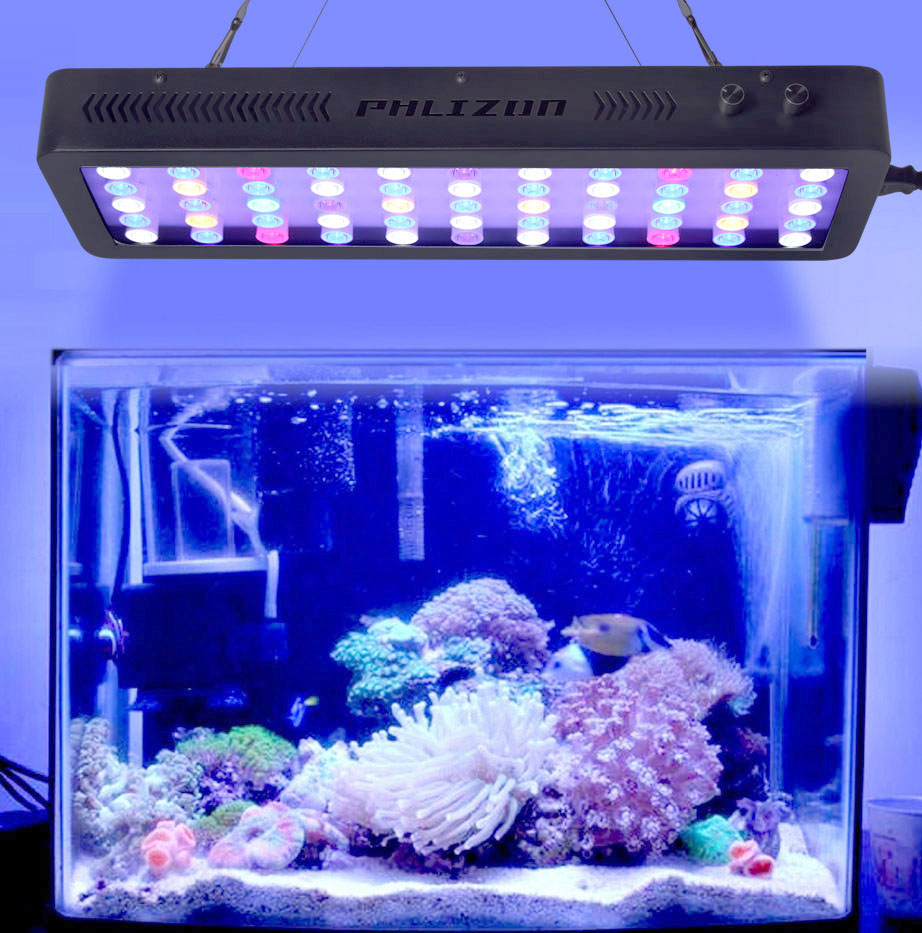
Our Company
Philizon Advantages
Professional: we are professional LED Grow Lights and LED aquarium light manufactuer here in China,you will get Professional and High quality LED Grow Lights and Coral Reef Led Aquarium Light from us and get good guarantee.
Cost-effective Price:we don`t have the lowest price,but the Coral Reef Led Aquarium Light you get from us really cost-effective,good quality & decent price.
Win-win situation:Long term business is our mission,we will provide good Coral Reef Led Aquarium Light and warming service to build a long-term business relationship with you
24/7 unlimted customer service: we are always here for you for your question,any question just email us or call us,we do our best to help you all the way.
Long term warranty: Don`t worry about the quality and we guarantee you 3years warranty for all the LED Plant Grow Light and coral reef led aquarium light.
Best buying experience: you will get the tiptop serive you have ever had,just have a try and you`ll see.
Trade Terms
Payment: T/T, L/C, Paypal, 30% deposits before production, 70% balance to be paid before deliverying(Western Union are welcome)
Sample will be delivered within 7 working days.
Discounts are offered based on order quanlityes.
MOQ:sample order are acceptable
Delivery ways:DHL,UPS,FedEx,TNT, door to door,by sea,by air,etc.
Philizon enjoys a high reputation in grow led lamp and led aquarium light fields throughout Europe and America,Philizon also insists on taking high technology to design the newest&best led Grow Light and aquarium light constantly as the market request. Our R&D team with more than 10 people has rich experience in appearance design, electronic structure,heat dissipation simulation analysis,optical lens design,light control system etc.Most of our hydroponics full spectrum led grow lighting and Coral Reef Led Aquarium Light are private modules,we have 10 more design patent and utility model patent till now.
Warmly welcome to take a visit on our factory at any time and we will pick you up at the airport or hotel as you request.
Aquarium Led Light,Smart Led Aquarium Light,Smart Aquarium Light,Aquarium Led Light
Shenzhen Phlizon Technology Co.,Ltd. , https://www.szledaquariumgrowlight.com